In das Dach unseres Tw 276 sind inzwischen viele weitere Arbeitsstunden geflossen, für einen neuen Beitrag gab es allerdings zunächst nur wenig zu sehen.
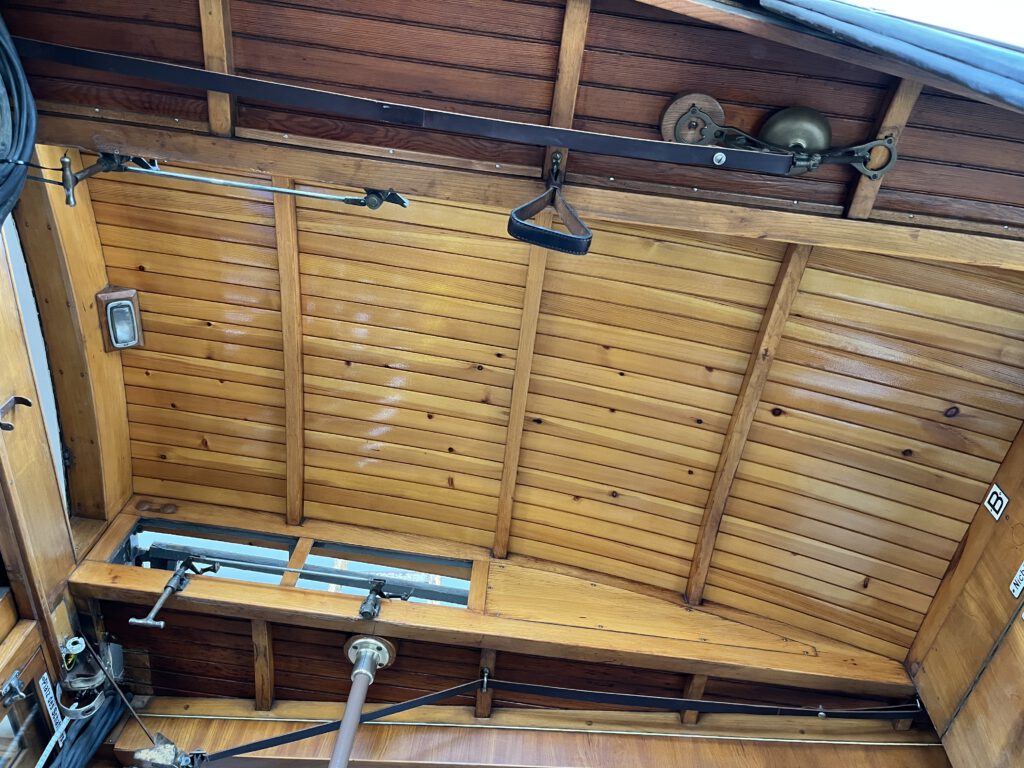
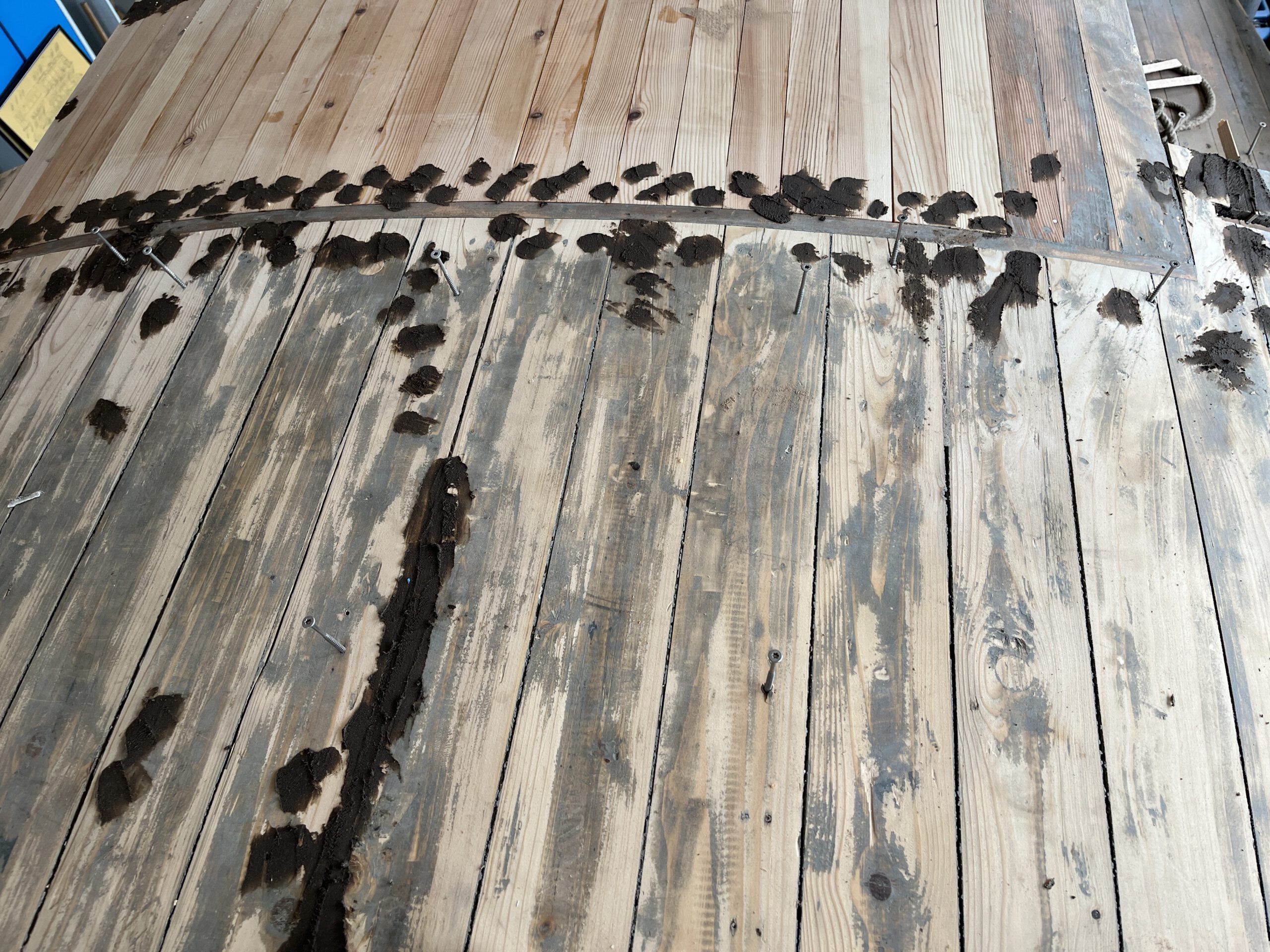
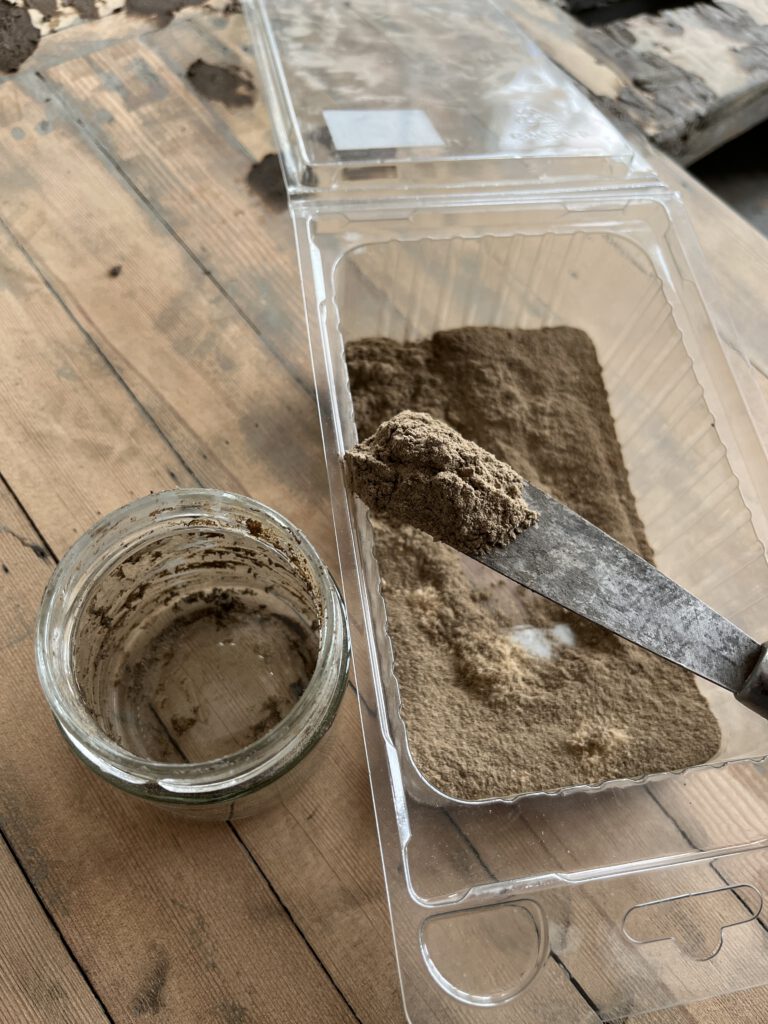
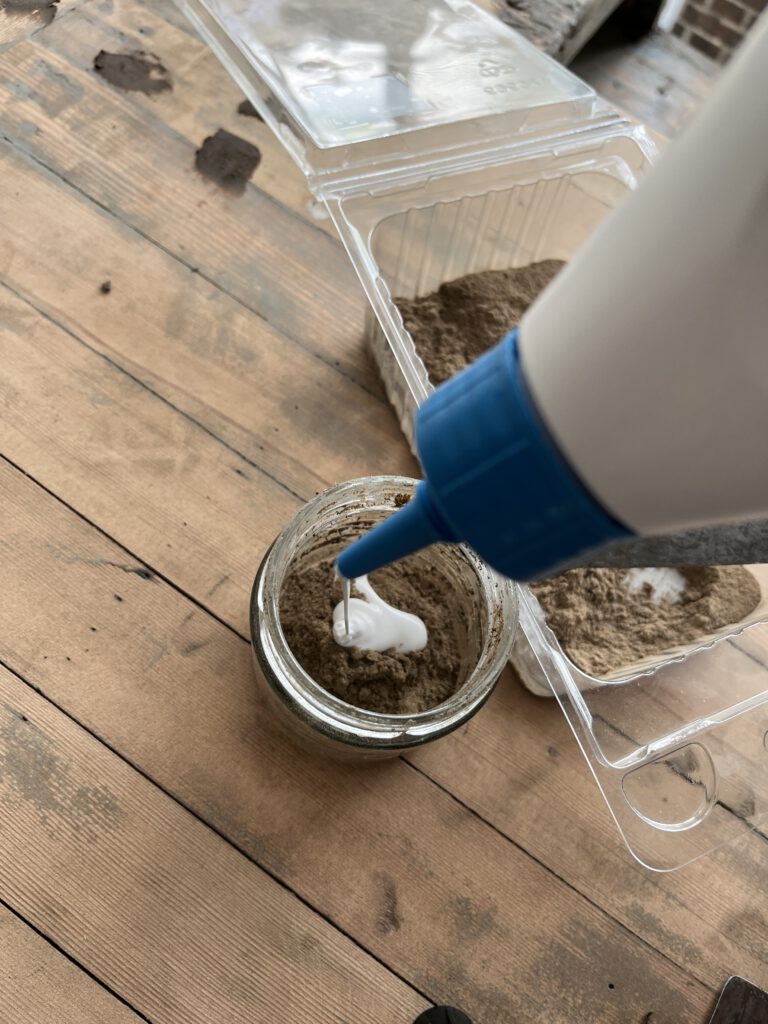
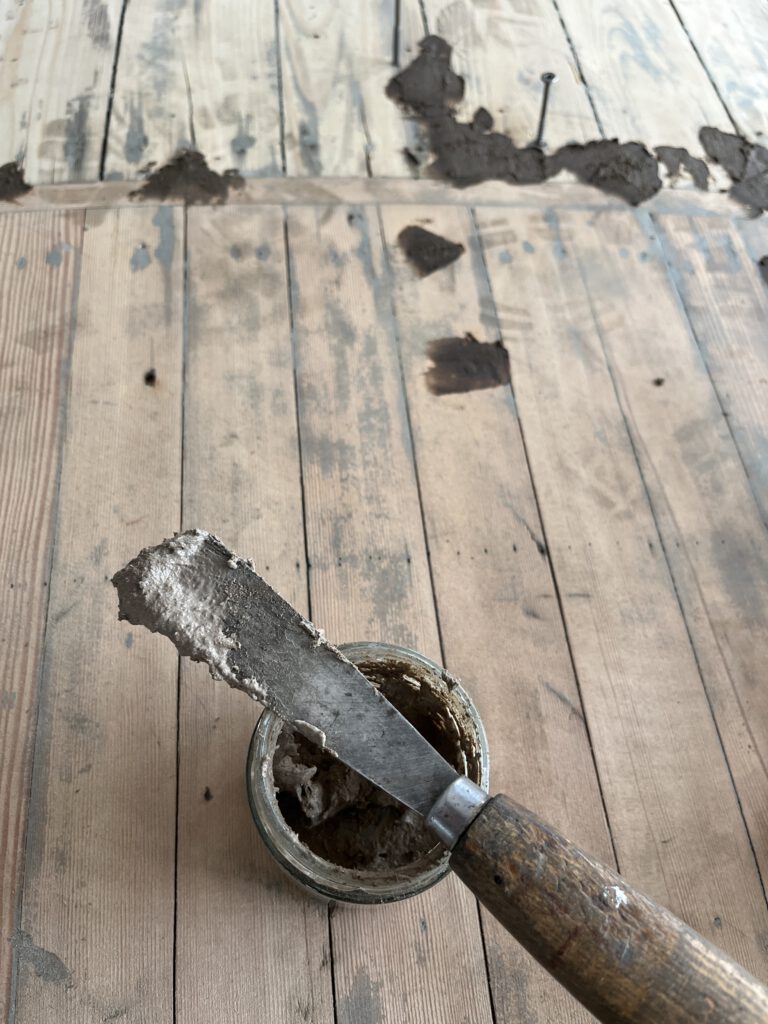
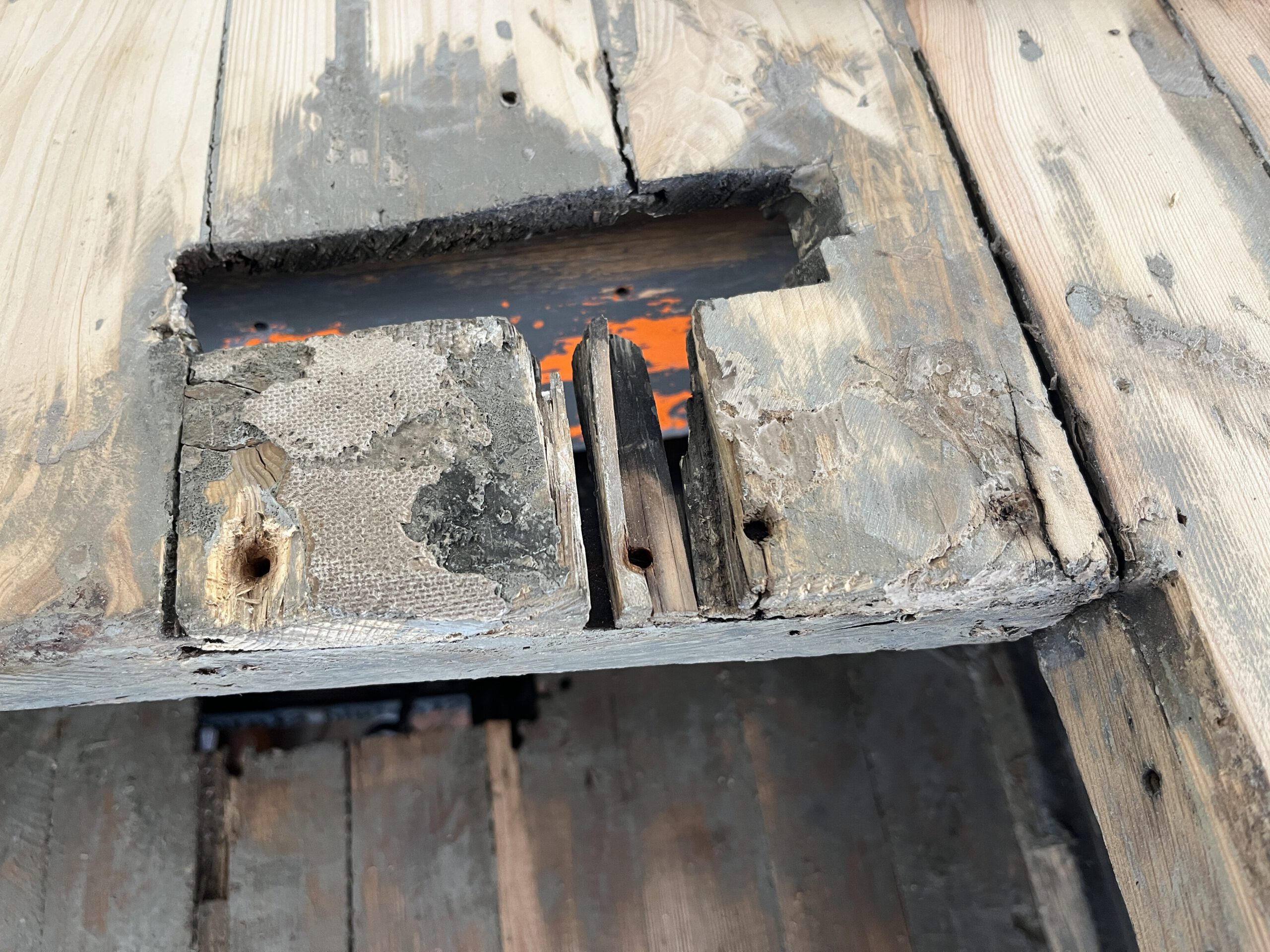
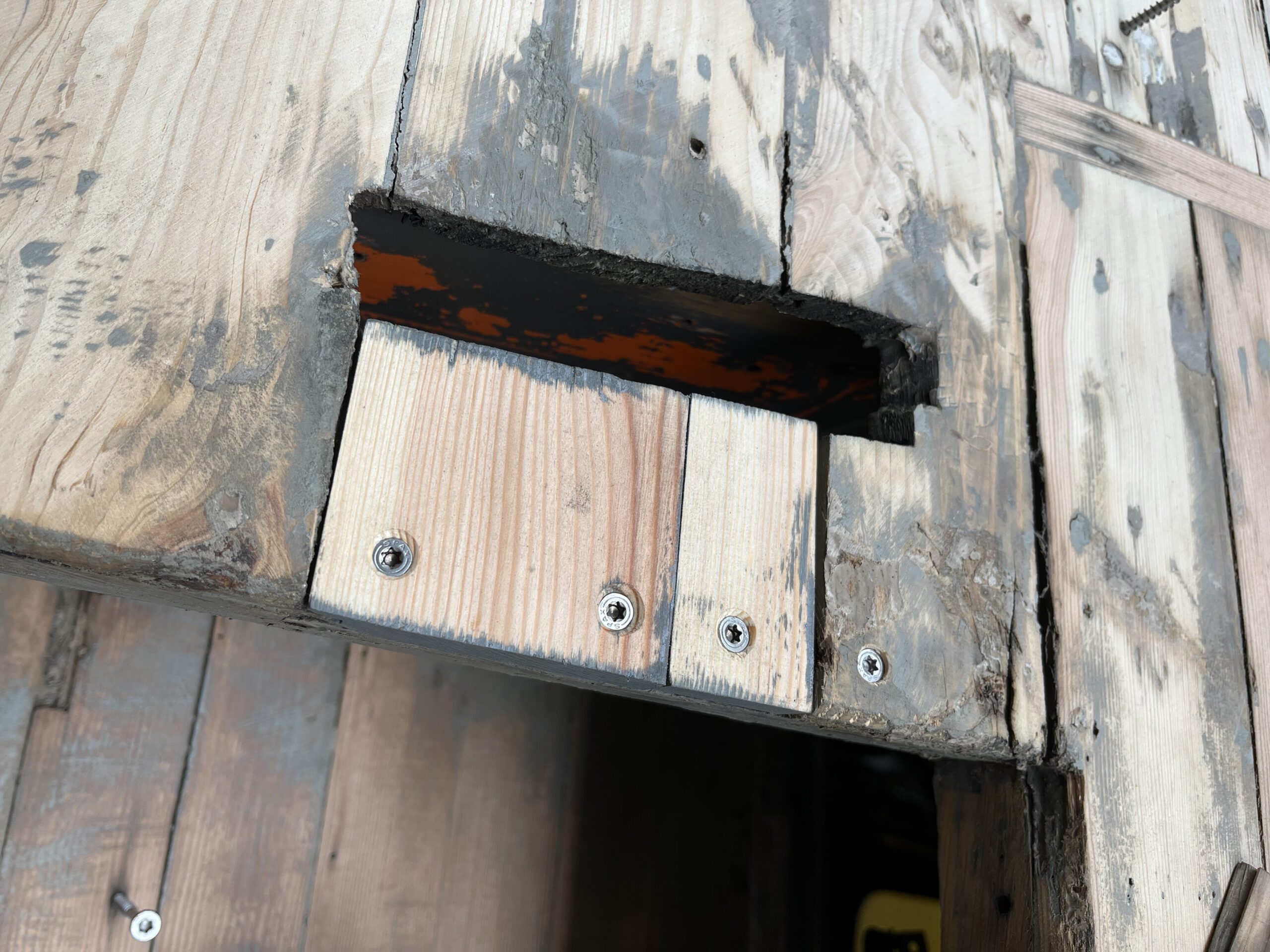
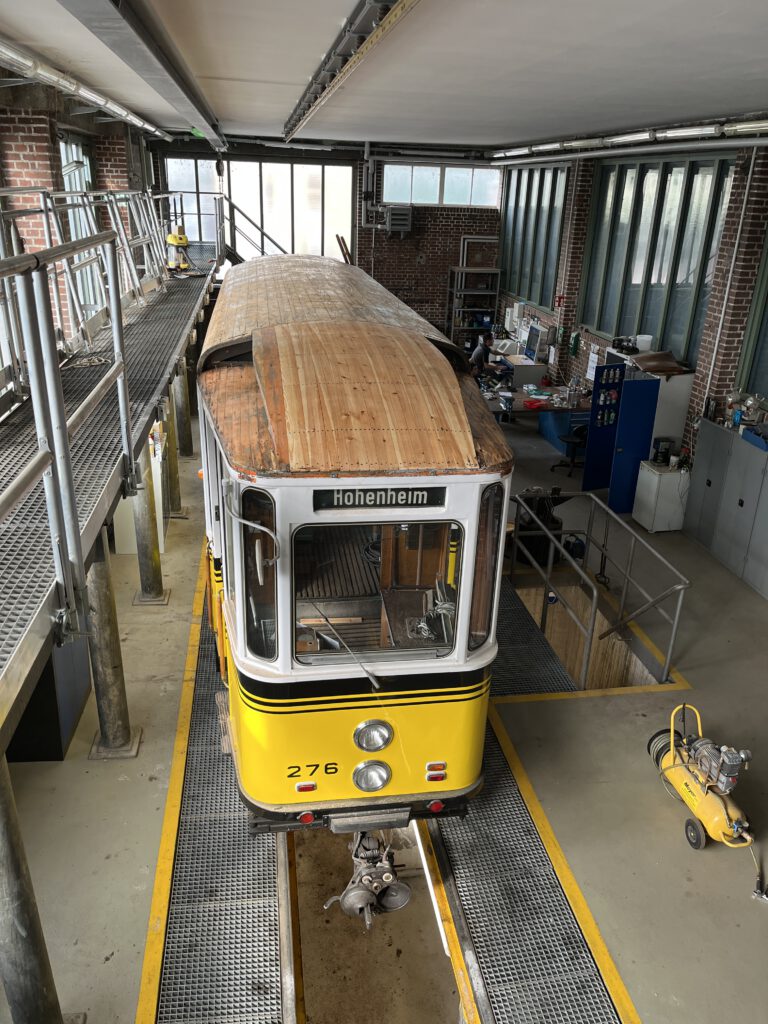
Stuttgarter Historische Straßenbahnen e.V. – Blog
Der Blog mit aktuellen Nachrichten
In das Dach unseres Tw 276 sind inzwischen viele weitere Arbeitsstunden geflossen, für einen neuen Beitrag gab es allerdings zunächst nur wenig zu sehen.
Es gibt Neuigkeiten zu den Arbeiten am Dach unseres Tw 276, so dass uns ein kleines „Update“ angebracht erscheint.
Bei über 20 m Straßenbahn gibt es natürlich viele Baustellen, die teilweise parallel bearbeitet werden. Am DoT4 917 konnten wir nun im B-Teil die abgelaufenen Fußbodenleisten demontieren. Diese werden durch Neuanfertigungen ersetzt.
Außerdem wurden die letzten Wochen durch die SSB die neue Dämmung für das Dach montiert. Somit können wir demnächst mit der Montage der Deckenplatten beginnen. Dies wird aber erst geschehen, wenn der Fußboden überarbeitet ist, damit die neuen Deckenplatten nicht gleich staubig werden.
Außerdem gab es bereits eine kleine „Hochzeit“. Im Schienenfahrzeugbau ist mit „Hochzeit“ die Montage von Wagen und Fahrgestell gemeint, was einen großen Schritt zur Fertigstellung von Schienenfahrzeugen darstellt. Beim DoT4 konnten wir nun die beiden Karusselle (Gelenkportale) mit dem Mittelteil verheiraten. Dies ging erstaunlich gut von der Hand.
Der Triebwagen 418 feiert seinen 100. Geburtstag!
Zwischen Mai und Oktober 2025 veranstalten wir mehrere Fahrtage unter dem Motto „Straßenbahn fahren (fast) wie vor 100 Jahren“. Weitere Informationen finden Sie unter www.shb-ev.info.
Fünf Jahre ist es inzwischen her, dass die Fahrmotoren unseres KS-Triebwagens 749 zur Prüfung und Instandsetzung aus dem Fahrgestell ausgebaut worden waren. Zwischenzeitlich haben wir die mechanischen Teile des Fahrgestells aufgearbeitet und neu lackiert, und auch die Motoren waren längst wieder einbaubereit – Personalmangel und andere, dringendere Aufgaben ließen den geplanten Zusammenbau jedoch immer wieder nach hinten rutschen. Anfang April war es aber endlich soweit: Mit tatkräftiger Unterstützung eines kundigen Fachmanns von der Woltersdorfer Straßenbahn ging es ans Werk.
Liebe Freunde der historischen Straßenbahnen, Ihr werdet bemerkt haben, dass es in den letzten Wochen hier im Blog etwas ruhiger geworden ist und es keine „Werkstatt-Updates“ gab. Der Grund ist einfach: Wir haben eine weitere Baustelle, die unsere Zeit bindet. Ausgangspunkt war ein eher kleiner Unfall unseres Tw 276, ein Bügelschaden durch ein Hängenbleiben am Trenner des Hallentors im Juni 2024, wobei Trümmerteile ein Loch ins Wagendach schlugen. Die Auswirkungen dieses an sich nicht großen Schadens wurden erst deutlich, als wir im Frühherbst begannen, eine Reparaturtechnologie auszuarbeiten. Die wahrscheinlich aus den späten 1950er Jahren stammende Dachbespannung aus Segeltuch erwies sich als brüchig und stellenweise bereits so löchrig, dass eine einfache Reparatur mit Flicken nicht mehr als sinnvoll anzusehen war. Im Ergebnis war damit klar, dass alle Dachaufbauten demontiert werden mussten, um anschließend das Fahrzeugdach neu bespannen zu können. Dies wiederum würde absehbar dazu führen, dass manche Teile der hölzernen Dachaufbauten aufgrund ihres Zustands die Demontage nicht ohne Zerstörung überstehen würden, also anschließend neu anzufertigen sind. So kommt man „nebenbei“ zu einer weiteren Großbaustelle – aber es nützt ja nichts, der Wagen soll schließlich möglichst bald wieder fahren.
Nach dem Ende ihrer Nutzungsdauer werden Schienenfahrzeuge vereinzelt bei anderen Bahnen weiterbetrieben oder in Museen der Nachwelt erhalten. Die allermeisten von ihnen gehen allerdings mit der Verschrottung den Weg zurück in den Wertstoffkreislauf. Bei den Beiwagen der Reihe 1500 / 1600, welche zwischen 1954 und 1957 für die Stuttgarter Straßenbahnen AG (SSB) gefertigt wurden, war dies nicht anders. Von den 146 – liebevoll „Schiffle“ genannten – Wagen sind heute noch lediglich fünf Exemplare vorhanden. Drei davon gehören zum SSB-Museumsbestand (Wagen 1511, 1547 und 1605), der vierte ist als Wagen 24 (ehemals 1602) in der Obhut der Ulmer / Neu-Ulmer Nahverkehrsfreunde e.V..
Der Beiwagen 1584 bekam nach seiner Abstellung 1976 einen ganz anderen Weiterverwendungszweck: Als Gestaltungselement eines neu angelegten Gartencenters in Stuttgart-Vaihingen.
Heute zur Ausstattung des Pflanzenhofs Vaihingen gehörend, wurde der Wagen in den Jahren 2000 und 2005 überarbeitet. Im Sommer wird er als Café für Veranstaltungen genutzt und soll zukünftig auch als Tagungsraum dienen. Hierzu finden aktuell Umbauarbeiten im Innenraum statt.
Weitere Informationen: https://www.pflanzenhof-vaihingen.de/ueber-uns/unsere-strassenbahn
Weitere Informationen zum Wagen 24 in Ulm: https://www.unf-ulm.de/fz/2-Bw24.html
(Für die verlinkten Internetseiten wird keine Haftung übernommen.)
Einsteigen und Geschichte erfahren: https://www.shb-ev.net/web/index.php?id=8
Damit nicht nur der Blick aus dem Fenster, sondern auch (von innen) auf das Fenster attraktiv ist, wurden beim Bau der T2-Triebwagen in den 1950er Jahren Fensterrahmen aus Mahagoniholz angefertigt und mit Schellack seidenglänzend lackiert. Dies orientierte sich damals an der Auswahl von Materialien und Farben der übrigen Innenausstattung. Als ab 1965 der Umbau von T2 zu DoT4-Triebwagen wie unserem Tw 917 erfolgte, behielt man innen das Gestaltungskonzept der Spenderfahrzeuge bei, nur im neuen Mittelteil übernahm man das Design der inzwischen ausgelieferten 350 GT4-Triebwagen der SSB.
Somit steht bei der Restaurierung unseres Tw 917 nun auch die Aufarbeitung der hölzernen Fensterrahmen an. Davon hat der gesamte DoT4 so einige, nämlich insgesamt 26 Stück.
Die Sitz- und Rückenpolster im DoT4 werden von Stahlrohrgestellen gehalten, die in allen Fahrzeugen der Generationen T2/Bo, GT4 (vor dem Umbau zum GT4-2000) und eben DoT4 baulich identisch sind. Auch ältere Fahrzeuge erhielten diese nachträglich im Rahmen von Modernisierungen, wie z. B. unser Gartenschau-Tw 851. Nun sind in so einem DoT4 allerdings mehr als 20 solcher Gestelle in unterschiedlichen Ausführungen montiert, reichlich Arbeit für die Museumswerkstatt.
Bei unserem in Restaurierung befindlichen Tw 917 wurde durch die SSB die Komplettierung des B-Fahrgestells abgeschlossen. Verkabelung und Korrosionsschutz unter dem B-Wagenkasten sind ebenfalls fertig, also konnten Wagenkasten und Fahrgestell nun wieder zusammengeführt werden.